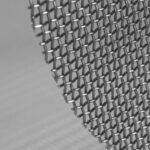
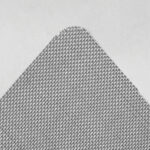
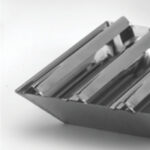
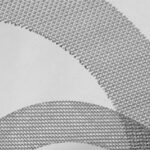
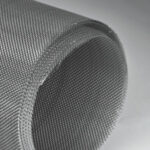
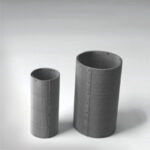
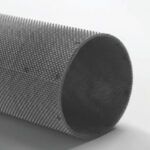
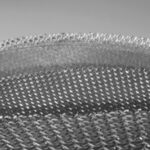
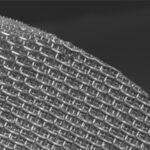
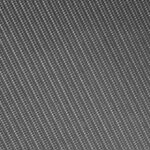

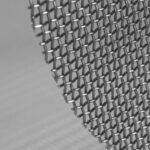
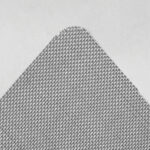
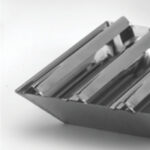
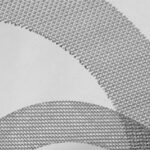
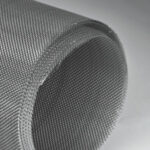
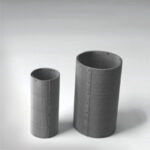
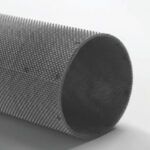
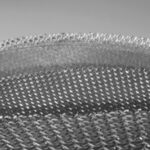
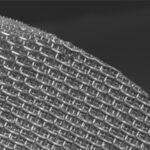
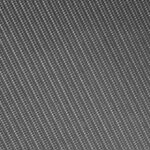

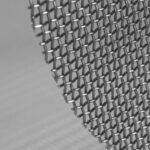
The Ultimate FAQ Guide
If you have any questions about the extruder screen, you will find the answer right here. Keep reading to learn more.
A multilayer extruder screen pack is made from several screens of different mesh sizes by welding them together. It has the finest screen wire in the middle of the pack while the larger mesh sizes are on the outer sides, which prevents the screen pack from accidentally being installed backwards. Multilayer screen packs are sturdy, strong, and offer convenience when processing substances. It also eliminates operator errors by installing the right sequence.
There are several types of Extruder Screens:
- Circular Screen
- Multilayer Circular Screen Pack
- Multilayer Cylindrical Screen Pack
- Multimesh Circular Screen
- Designer Screens (Kidney Shape/Oval Shape/Rectangular Shape)
- Filter Discs
The common mesh types of extruder screens include:
- Plain Square Weave
- Plain Dutch Weave
- Twilled Dutch Weave
Extruder screen materials are mainly stainless steel and nickel alloys. Stainless steel packs are much more resistant to rust than others. When choosing packs you must consider their working environment. SS 304 L has a higher resistance to elements like corrosion, rust, high temperatures and pressure to provide the best results.
Some of the qualities to look for in an efficient extruder screen:
- Durability of the extruder screen.
- Resistance to elements like corrosion, rust, and high temperatures.
- The number of screen mesh per square inch.
- Percentage of the opening of the mesh.
- Weave types like Plain weave, Dutch weave, Twilled weave etc.
Here are the key advantages of extruder screens:
- Corrosion and anti-abrasive resistance.
- An optimum cost-performance ratio.
- Good quality control during the filtration process.
- Durability with a robust structure.
- Diverse shapes and sizes.
It is not possible to clean and reuse the Multilayer screen pack. This is because the flow of products can make the mesh warp torn and twisted thereby lowering their efficiency. Whereas Single layer extruder screen can be clean and reused again.
The replacement period depends on the filtration process of your application. Also, the amount of dirt in the melt, or the number of impurities you need to filter out influences the replacement period. When filtering out clean melt substances, they can last for many days or weeks with no changes or replacements. Besides, you need to replace extruder screens that filter dirty materials every hour.
A guide to the importance of using screens in your extrusion process:
Almost all extrusion processes use melt-through wire mesh screens that filter out any contaminants before passing through to a die. The screens are held together by breaker plates, which have holes or slots and these form a seal between the extruder and the die.
Wire mesh screens can also improve mixing and protect gear pumps from being damaged by hard contaminants. Fine meshes make the most suitable shields for gear pumps that have small clearances.
Typically, screen packs will place the coarsest screen against the breaker plate and the finest screen facing the screw. This prevents the screen from
Choosing appropriate screens for an extrusion process involves striking a balance between filtration needs (removing more contaminants) and overheating. Finer screens get more contaminants out, but they also raise back-pressure in the extruder, which requires more power from the motor and, thus, creates more frictional heat. Barrel cooling may help, but it isn’t efficient because it raises viscosity on the barrel wall and makes the motor work even harder, putting back some of the heat taken out by the coolant. Finer screens also need to be changed more frequently.
Screens are often put in as a screen pack, with two, three or more screens of different meshes. Most packs have the coarsest screen up against the breaker plate to support the others, but putting it in “backward” also works, as the bigger particles get caught first and never reach the finest screen. The packs may be premade and put in baggies until needed, spot-welded together to ensure they stay in the right order or may have a crimped aluminium edge, which holds the screens together while serving as a gasket to prevent leakage.
There are varying applications of extruder screens in various fields including:
- Plastic Recycling
- Pharmaceutical
- Agriculture
- Rubber Tyre & Tube
- Woven Sack
- PVC Wires & Cables
- Reprocess Granules
- PVC Fittings
- Plastic Sutli
- Plastic Roofings
- Non-Woven Fabric
- Multilayer Film
- Laminations
- Master Batch
- Moulded Furniture
- Bopp Films
- Air Bubble Film
- Disposable Products
- Box Strapping
The price of an extruder screen will depend on several factors like:
- Shape
- Size
- Material
- The number of layers.
- Unique processing requirements.
- Quantity of extruder screens.
Yes, just give us your specification and will deliver a free sample as per your requirement.